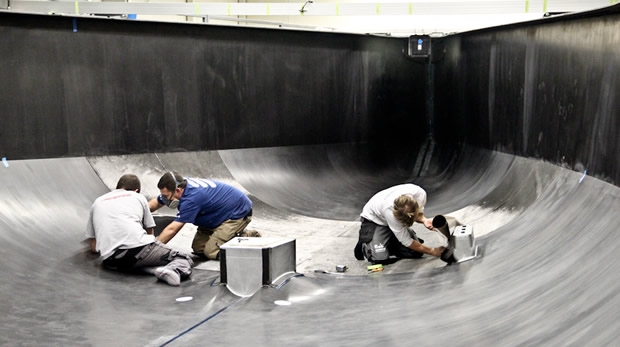
Photos; Mark Somerville / Persico
Fonte: The Daily Sail
A couple of significant milestones have been passed in the build process for the Volvo Ocean 65 at boatyards in Italy and France.
At Persico in Italy, lamination of the outer skin of the first hull being produced has now begun, while at Multiplast in France the first carbon layer for the first deck has been completed.
"We have about 20 guys working on this," said Mark Sommerville, Operations Manager for the work going on at Persico. "The final layer of the outer skin went down on Wednesday and we also have a team thermoforming the foam core."
The mould has been produced with an infusion system so that the laminate is less porous, takes in less air and is more stable over a long period of time. The steel structure that supports and strengthens the mould has also been calculated and tested to remain solid throughout the curing process.
The 12.5mm thick mould, for which around 1,400kgs of resin have been used, is cut longitudinally to facilitate the unplugging and includes removable flanges at the top sides that create the structure where the deck will be joined to the hull and the special recess for the keel ram.
“It will take eight weeks to produce a hull, fitted with the bulkheads provided by Decision SA that will make the structure stiffer and ready to be shipped to Green Marine,” said Marcello Persico, Managing Director of Persico's marine division. “For the time being we have only built one mould but we would be able to make a second one, using the existing model, should the Volvo Ocean Race need to increase production as more teams order a boat. Also, we are committed for two editions of the race and that makes it vital to be able to use the mould on a long term span.”
The huge structure will be carefully cured with the help of several powerful burners that will take the inside temperature to 80-90°.
“The curing process has to be dealt with with extreme care,” says Sommerville, an expert from New Zealand who has been working with the international staff at Persico for several years. “The temperature inside the oven needs to increase and later decrease at a very steady and accurate pace, 12° per hour, because any sharp variation could compromise the process, the resin could go soft and not catalyse properly. It takes approximately six to seven hours to get to the right temperature and back. During this phase we work on shifts in order to ensure the process is monitored constantly.”
Meanwhile at Multiplast in Vannes, France the Volvo Ocean 65 deck’s first carbon layer has just been finished. The first deck should be completed by mid-February and delivered to Green Marine to be assembled.
“We just finished cooking the first carbon skin of the first deck. Every deck will be cooked four times: the outer skin is cooked first to be painted (this doesn’t make sense), then a second time for the honeycomb and foam core and a third and fourth time for the inner skin,” confirmed director Yann Penfornis, whose enthusiasm for the project is obvious.
“We are therefore four weeks away from taking the first deck out of the mould. Then we will have six to seven weeks of pre-piercing the deck fittings for grinders, organisers and deck stiffeners. The first deck will be delivered mid-February to Green Marine and we will be working on the second deck by then. From then on a new deck will be produced every seven weeks.”
Multiplast is tackling this technical challenge with a 30-person dedicated team. Their 200°C oven also allows the carbon and core components of the deck to cook more efficiently.
“Making sure it’s a one-design product is a challenge,” explained Sommerville. “Here at Multiplast we know how to build 20m boats. But building eight identical boats with only a few kilos of difference does require a good traceability with processes and plans. Each piece of foam has to be weighed. The sailors won’t have any excuse; they need to race on equal terms. We don’t want to hear them saying the boat three is faster than boat five.
“The second challenge is delivering a deck every seven weeks. Such big pieces need good organisation and very detailed planning. We are working on it, but we cannot allow ourselves to fall asleep. We have to make eight boats in two years and that’s the power of the consortium: the four boatyards are strong ones and trust each other. We will get there, but we cannot afford to be late. We need
the first one to be on time if we want to deliver the eighth one on time.”
The first boat off the production line is expected during late June 2013. After that the plan is to have each new boat sailing within three to four days of leaving the boatyard, but before passing this even bigger milestone, there are still a lot more deadlines to meet.
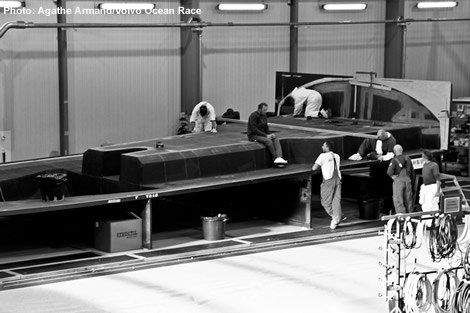
Sem comentários:
Enviar um comentário